BASF pioneers world’s first electric steam cracking ovens
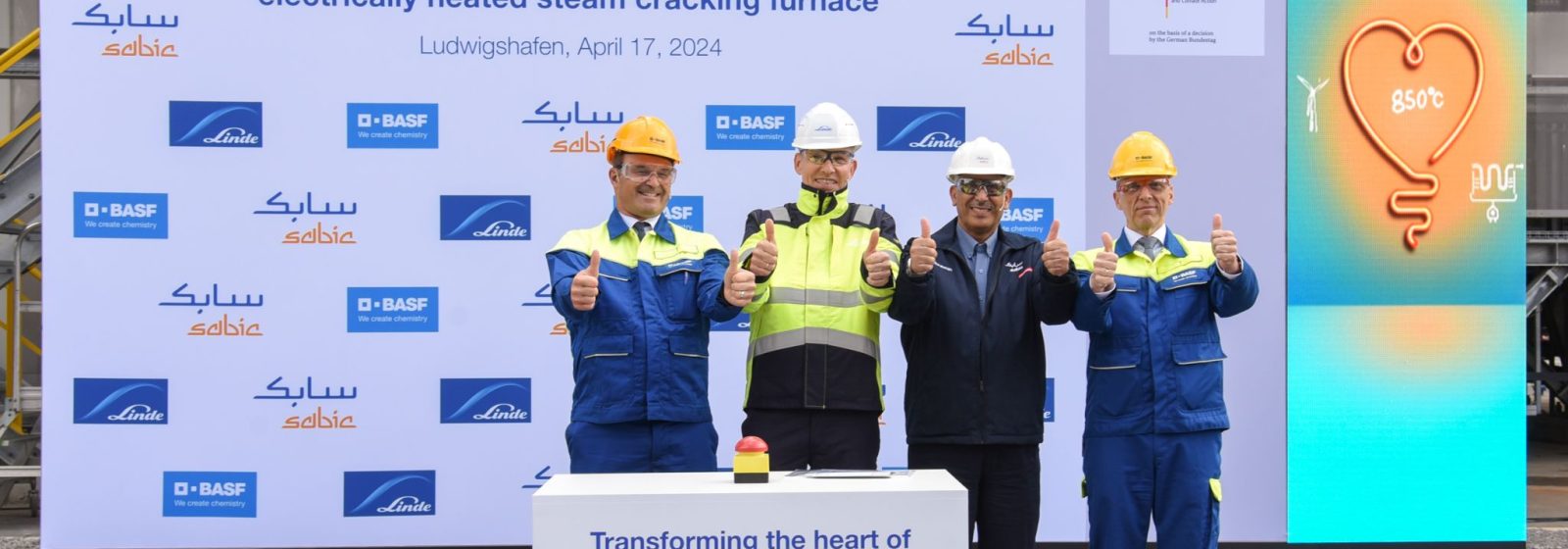
Together with Middle East’s largest petrochemical company SABIC and industrial gas and engineering company Linde, German chemical giant BASF inaugurated the world’s first demonstration plant for large-scale electrically heated steam cracking furnaces.
In March 2021, the three companies gave the go-ahead for the development and construction of the electrically heated steam cracking furnaces. After three years of development, engineering and construction work, the demonstration plant can now be commissioned at BASF’s Verbund site in Ludwigshafen, Germany.
Reducing emissions by 90%
Steam crackers play an important role in the production of basic chemicals and require a significant amount of energy to break down hydrocarbons into olefins and aromatics. Usually, the reaction is carried out in furnaces at temperatures of around 850 degrees Celsius. Until now, these temperatures have been achieved with conventional fuels such as gas.
The demonstration plant now aims to demonstrate that continuous production of olefins is possible using green electricity as a heat source. By using electricity from renewable sources, the new technology has the potential to reduce CO2 emissions from one of the chemical industry’s most energy-intensive production processes by at least 90% compared to conventional steam crackers.
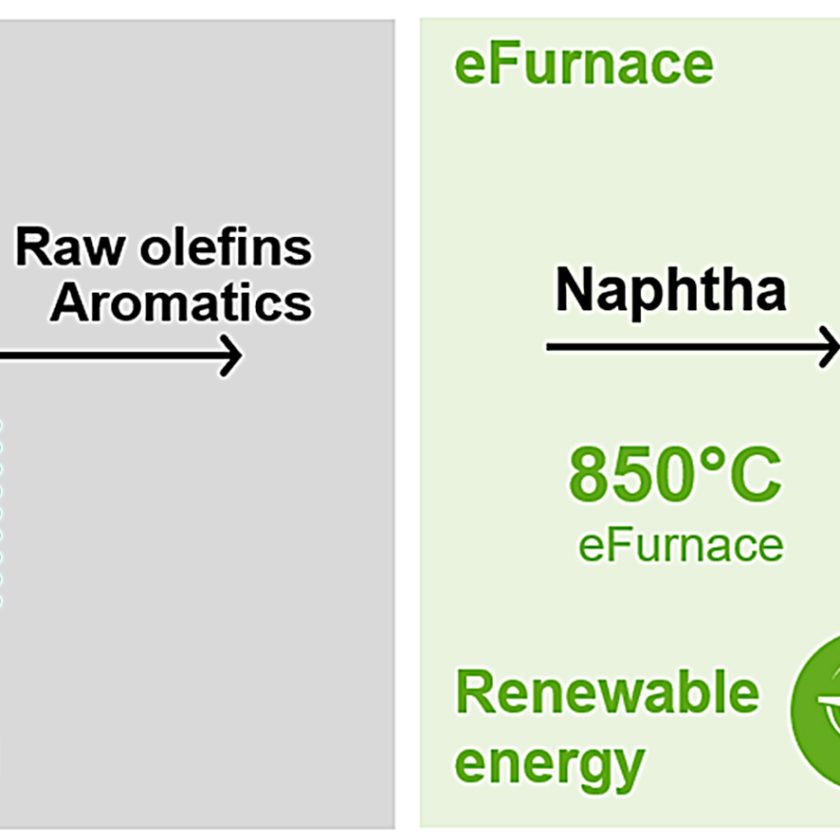
Integrated demo plant
The demonstration plant, which produces olefins such as ethylene, propylene and possibly higher olefins from saturated hydrocarbon feedstocks, is fully integrated into the existing steam crackers in Ludwigshafen. By actively deploying the demo plant immediately, BASF aims to gather data on the behaviour of materials and processes under commercial operating conditions. Later, that innovative technology can then really be developed to industrial market maturity.
The company chose to test out two different heating concepts. While in one furnace direct heating applies an electric current directly to the breaking coils, in the second furnace indirect heating uses radiant heat from heating elements placed around coils.
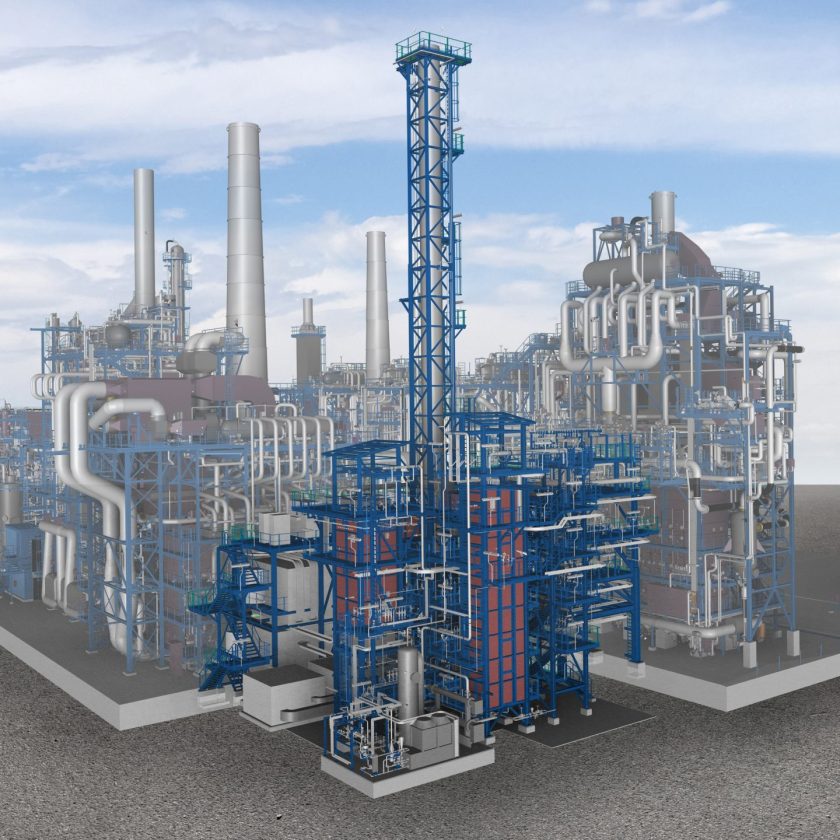
Decarbonisation in industry
Together, the two electrically heated furnaces will produce about 4 tonnes of hydrocarbon feedstock per hour and consume 6 megawatts of renewable energy. To support the development of the new furnace technology, the project received EUR 14.8 million from the German Federal Ministry for Economic Affairs and Climate Action under the ‘Decarbonisation in Industry’ funding programme. The programme supports energy-intensive industries in Germany in their efforts to become carbon-neutral.
“With the development of electrically powered steam cracking ovens, we are getting our hands on a key technology that will help to significantly reduce greenhouse gas emissions in the chemical industry,” said BASF CEO Martin Brudermüller. “It fills me with pride and joy that we have achieved this success together with our partners SABIC and Linde. The demonstration plant in Ludwigshafen will provide us with valuable information for the final step towards the industrial application of the technology.”
Verbund sites
BASF is integrating the electric steam crackers into its existing Verbund site in Ludwigshafen. By using the Verbund system, BASF thus passes through complete value chains from basic chemicals to consumer products. Chemical processes use energy more efficiently, achieve higher product yields and also save raw materials. By-products from one process are used as starting materials for other processes. This saves raw materials and energy, avoids emissions, reduces logistics costs and exploits synergies. Of BASF’s 233 production sites, the six Verbund sites produce as much as 50% of the German chemical giant’s total volumes.